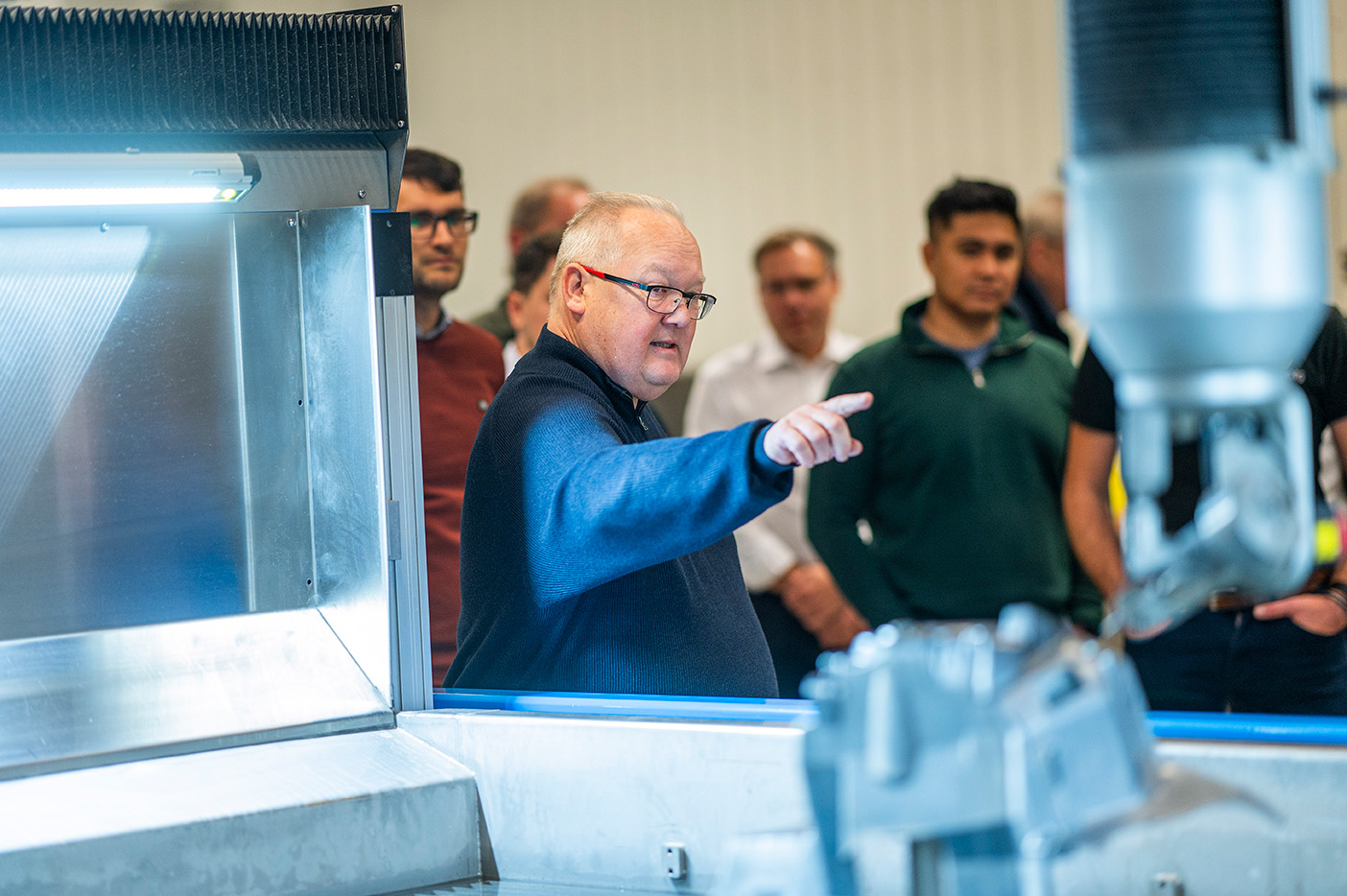
Finding the right micro waterjet for high tech ceramic parts
Technical ceramics & micro waterjet – Part 2
Competing for a CERN tender the Spanish company Nanoker Research S.L searched the world to find the right machine supplier. Specialists in technical ceramic material they needed to find a machine that could cut out fine precision parts using waterjet cutting technology. A search that brought them to Scandinavia.
How did the collaboration start?
In the fall of 2022, Water Jet Sweden was contacted by Alain Lennquist, CEO of KG Fridman AB, the Scandinavian representative of Nanoker Research S.L. They needed a price estimation for waterjet cut parts in a new technical ceramic material and sent over the technical specifications of the parts.
Tony Rydh, founder and CTO at Water Jet Sweden AB, with more than 40 years’ experience of waterjet cutting tells the story:
– We quickly realized that these parts needed to be cut with the fine abrasive micro waterjet technology. Since it is impossible to do calculations on a completely new material without test cutting, we contacted on of our clients in Sweden who has a machine that is specially designed and built for micro waterjet cutting. With their machine we could make some samples and perform cutting tests, Tony explains.
The client had recently installed a high-end NCM 10 Micro machine equipped with the new Alphajet TVL cutting tool. Since the parts needed a combination of fine abrasive waterjet and taper angle control, their machine was perfect for the task.
How to optimize waterjet cutting for new ceramic material?
The tests were successful and a couple of months later Alain Lennquist returned with a new task to solve.
– This time we needed to be more specific and developed an “optimized machinability index” for their material, tells Tony Ryd. A measure used to classify a material and its machinability.
To create an optimized machinability index, you begin with defining all available tool settings and process parameters, such as pressure, abrasive flow, type of abrasive, orifice size and focusing tube.
– You cut straight tracks where you, in small steps, adjust one parameter at a time. The setting where you cut the longest distance with the finest cut defines the index. You can often spot it visually, explains Mr. Tony Ryd.
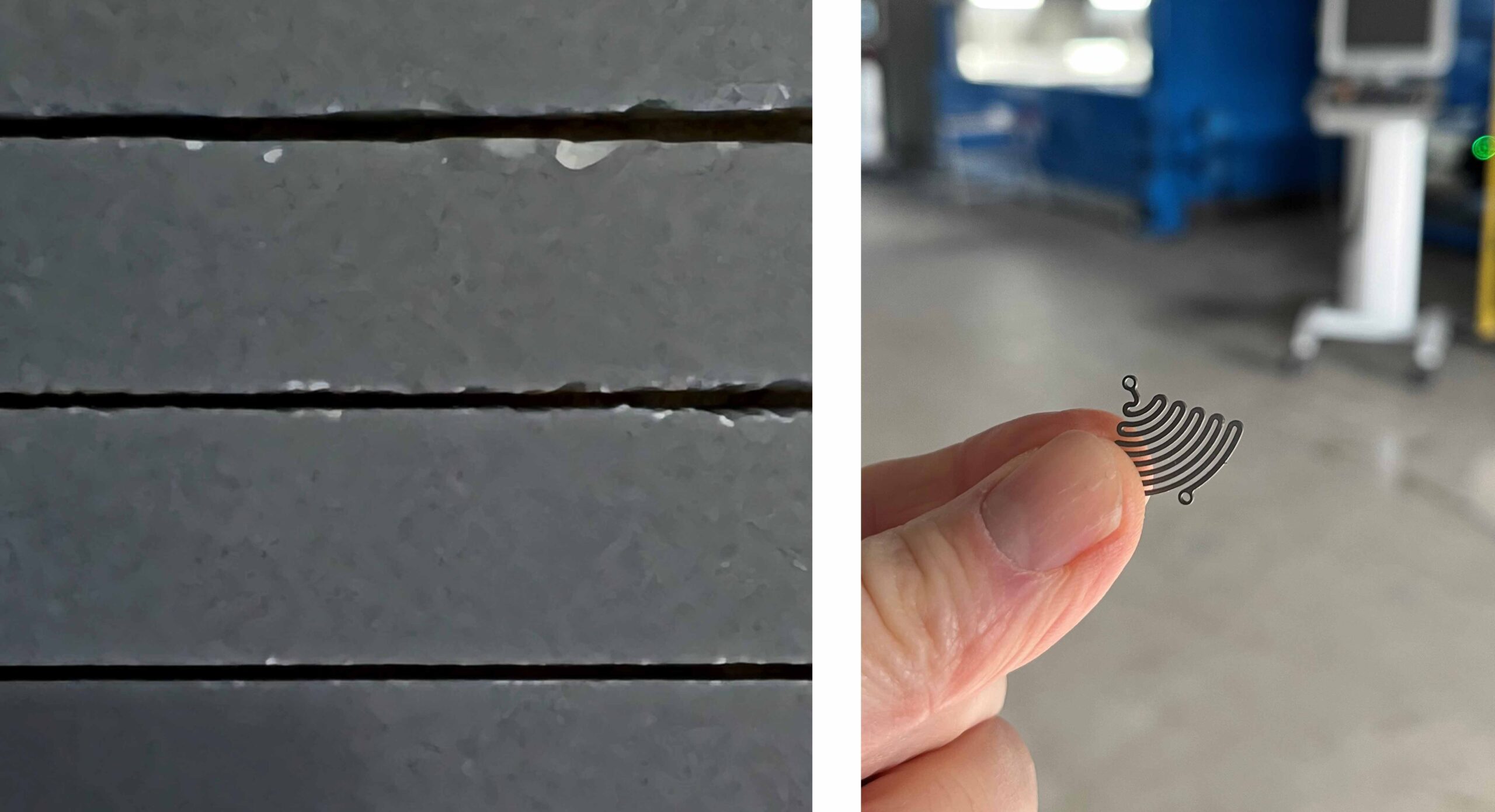
Picture: Left – Cutting tests to produce an Optimized Machinability Index for the new ceramic material. Right – Example of a part cut with micro waterjet technology.
Another benefit from the index-exercise was getting precise measurements of the angular deviation. With these measurements you can calculate how much angle compensation you need to meet the tolerance requirements. In a waterjet specific CAD/CAM software there is a list of TVL cutting tables available for the most common materials, but when you have a completely new material you need to create your own tables.
After getting the index each drawing was analyzed based on starting point, surfaces needing extra fine tolerance or less important surface roughness, to make the most efficient cutting program for each part. When optimizing the cutting program like this, the total cutting time will be significantly reduced, improving overall profitability of the fabrication.
Who can deliver a micro waterjet with TAC?
There are some waterjet machine manufacturers in the world that offer different kind of “micro cutting waterjets”, but after some market research there was only two suppliers with the technology required, i.e. true fine abrasive waterjet cutting with taper angle compensation capability.
– In the end there were only possible suppliers and both were from Scandinavia, tells Mr. Alain Lennquist. That’s why the project was led by us, being the Scandinavian representative of Nanoker. We also evaluated a waterjet supplier from USA. They have a good representative in Spain, but couldn’t fulfill the fundamental technical requirements. We identified a supplier in Switzerland too, but there were some uncertainties with that company, so we decided not to pursue, explains Mr. Lennquist.
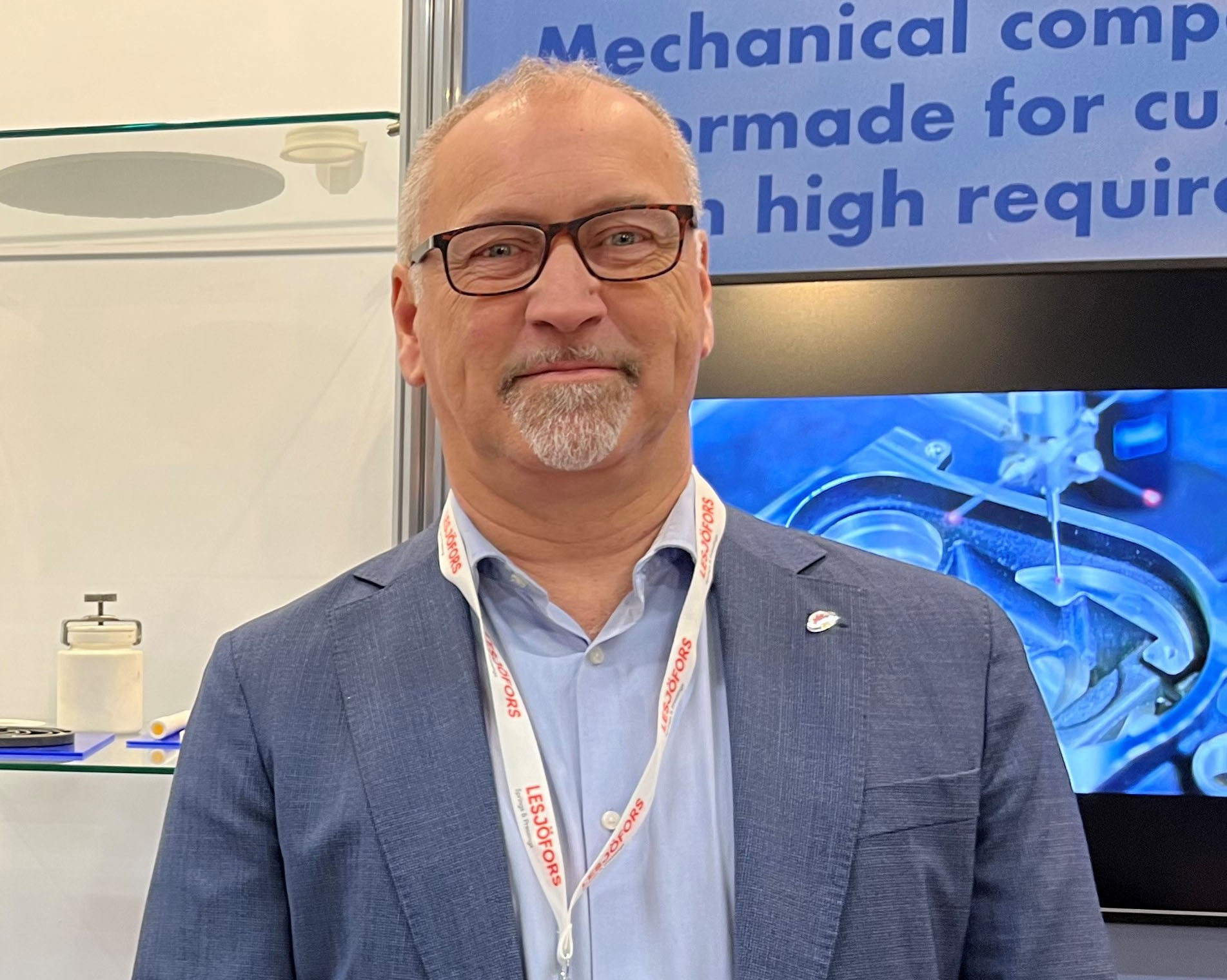
Mr. Alain Lennquist, CEO at Nanoker Scandinavian representative KG Fridman AB was leading the purchasing project.
Were there different approaches to the procurement?
The two selected suppliers were evaluated via test cuts and time studies. Both companies delivered correct parts, but in a slightly different manner.
– It is simple to fabricate 4-5 parts but to repeat and make thousands of parts with consistent quality is something else, explains Mr. Tony Ryd at Water Jet Sweden. High volume means much greater demands on both the machine and the fabrication process, Tony continues.
To prove repeatability of both the machine and cutting process Water Jet Sweden presented a pre-series of 400 parts instead of just a few parts. Every tenth part was evaluated in an electron microscope, measuring tolerances in hundredths of a millimeter and Ra-value for surface finish, to ensure requirements were met.
– When scaling up the volume our procedure identified variations in the material. This also helped Nanoker to fine-tune its own manufacturing process and achieve a more consistent quality of the ceramic material,” says Tony Ryd.
What became the preferred micro machine solution?
In the spring of 2023, the evaluation was finalized, and the choice fell on Water Jet Sweden and the NCM Micro machine with Alphajet TVL cutting tool.
The technology for micro waterjet cutting with fine abrasive was developed back in 2009 at Water Jet Sweden factory in Ronneby. In 2014 they launched their own micro waterjet; The NCM 10 Micro, a machine for very precise waterjet cutting with small tolerances.
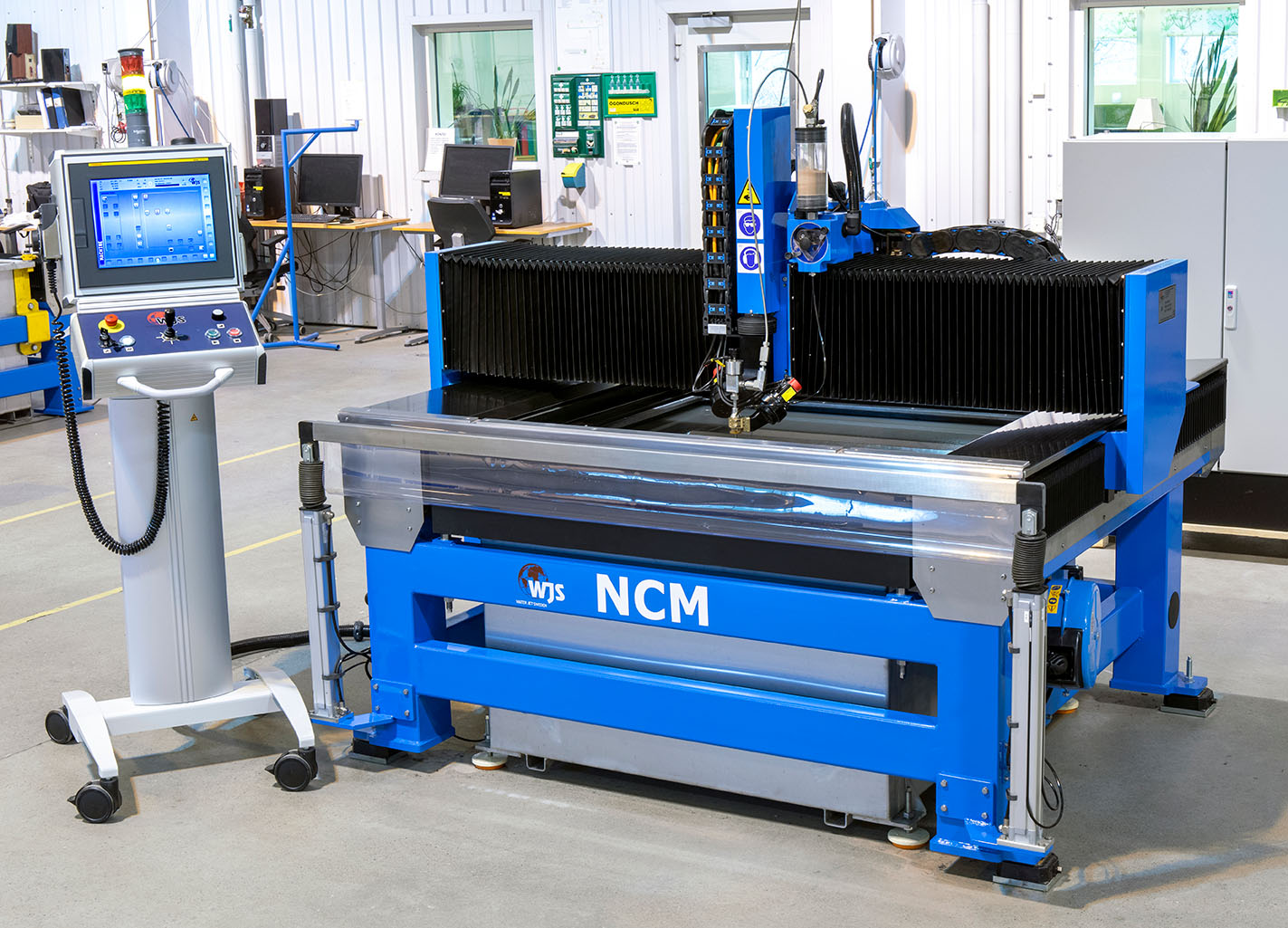
NCM 10 Micro, a high precision cutting tool for fine parts and micro components
The NCM 10 Micro machine has a number of unique features compared to traditional waterjet cutting machines:
- It is designed for Fine Abrasive waterjet cutting with 230-240 mesh abrasives and 200-400 micron focusing tube.
- It has software controlled abrasive feeding to sense feed rate, blockage and critical level in abrasive buffer.
- The table frame is made of an epoxy resin concrete for excellent stiffness, accuracy and absorption.
- Both X and Y motion systems has Renishaw Invar Scales with extremely low expansion coefficient and high resolution.
- It has a palletized cutting table with a wide range of fixturing possibilities. The Nanoker machine was equipped with a set of fixtures frames which some are optional features today.
- The stainless-steel catcher is rubber suspended to avoid vibrations. The catcher is also equipped with cooling elements to be able to control water temperature.
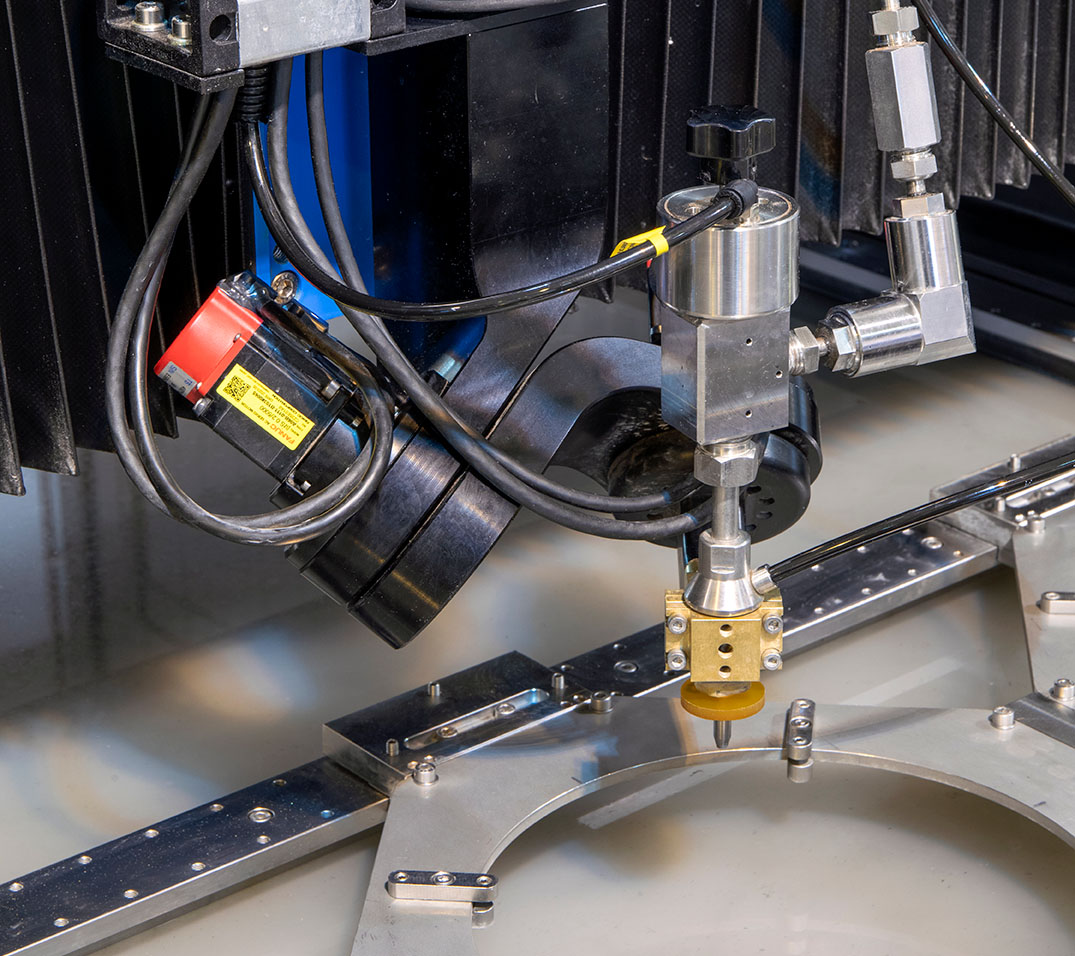
Alphajet TVL cutting tool and customized fixtures.
Above all this the Nanoker NCM 10 Micro machine is equipped with the new Alphajet TVL cutting tool, the next generation of taper angle control.
– We are proud to be chosen as a supplier for this project, tells Mr. Tony Ryd. We strive to be the obvious first choice for customers worldwide who seek solutions in water jet cutting where high quality, high technical content and high service standards are the basic elements.
During the fall of 2023 it was time to implement the new Micro waterjet cutting station at Nanoker site in Spain, quickly ramping up production to meet the high volume demands from CERN. Read more about that in our next article: Technical ceramics & micro waterjet, Part 3 – Implementing advanced industrial micro waterjet processing.
https://www.waterjetsweden.com/