Waterjet cutting turns waste into added value
Improved material recycling and usage with waterjet cutting
When processing expensive materials, it’s important to minimise waste. The following case shows how waterjet technology can produce Inconel cylinders, and save material in the process. By using waterjet technology to cut out holes instead of drilling them, the residual material can be stored, shaped and reused. This not only delivers better economy, but new product opportunities.
The results match the challenge
This case involves cutting holes up to 127 mm (3 inches) in diameter in 152.4 mm (5 inch) wide Inconel cylinders. The tolerance requirements are high and, until recently, processing has been performed by drilling. As the circumference of the hole is more than 50% of the material’s diameter, drilling means a good portion (36%) of the material is turned into waste.
The narrow incisions (1-1.5 mm) and fine kerf of waterjet cutting provides multiple recycling possibilities. Instead of simply drilling a hole, waterjet technology cuts out three separate pieces from the original material, much like stacking a Russian Matryoshka doll. The results are residual materials that can be recycled instead of wasted.
This is a precision process with a high potential for material savings. Success is dependent upon the correct cutting parameters, as well as the machine’s performance and precision. The challenge is to attain a result that lies within tolerance requirements, while maintaining accuracy over time.
A standard solution with a twist
The solution is based on a Water Jet Sweden H-model with a 2 x 1 m (6.6 x 3.3 ft) table surface. It’s a standard machine model, but it offers a complete workstation for all types of high-tolerance waterjet cutting in 2D.
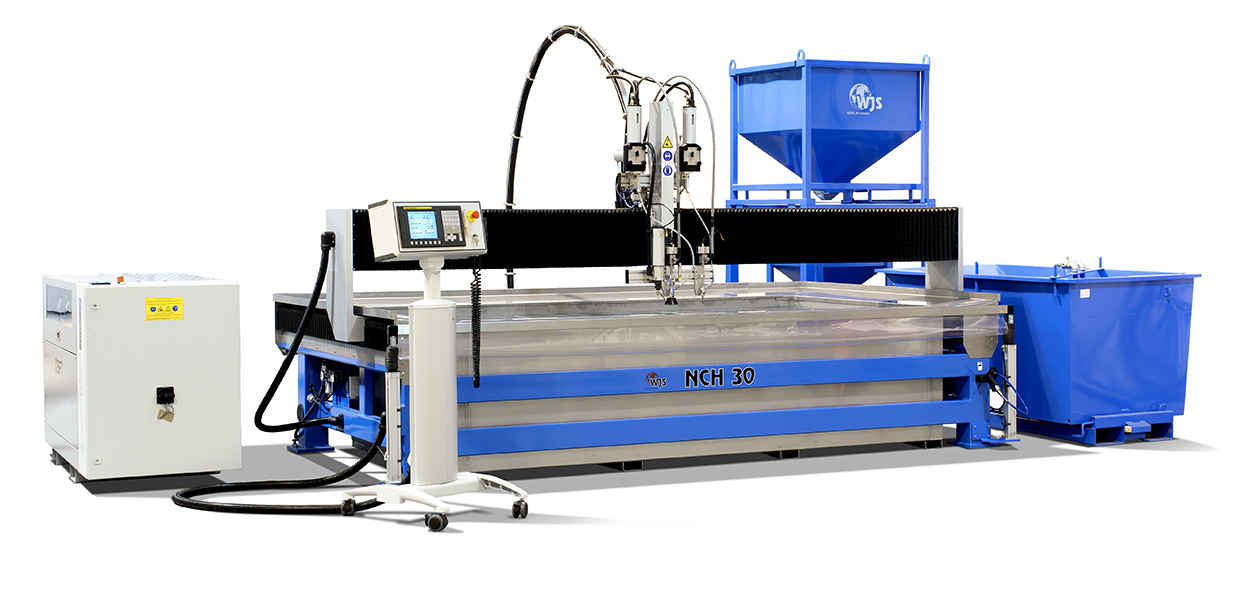
NCH 30, Water Jet Sweden
The 152 x 203 mm (5 x 8 inch) cutting items do not require a large work area. So, despite high-tolerance requirements, this standard machine size is more than adequate. It’s adapted to this particular machining process for easy and practical material management. Using a standard model also means that this solution is both cost-effective and proven, ensuring performance over time. The H-model comes with optional, extra-high cutting pressure. A KMT Pro 3 60 HP delivers 6200 bar of water pressure, resulting in faster processing and straighter cut surfaces, even with thicker materials.
The H-model is a true, high-performance CNC machine. It comes with FANUC OiF CNC control systems and a Fanuc 8.5″ touch-screen panel with an easy layout, especially designed for waterjet cutting.
Customised tank and fixtures
In order to cut the thick cylinders with up to 6200 bar, this H-model solution is enhanced with a customised tank, designed for an effective and smooth production process. The solution also includes extra splash guards on the side and a special nozzle cover to spread water horizontally. When piercing thicker materials this is important for the working environment, as water spray is often deflected. To ensure both high precision and repeatability, the tank is equipped with an integrated fixture system that consists of three parts; a fixture bench, a palette fixture and material holders.
The fixture bench is connected to the tank with special feet for improved support, and maximum stability and repeatability.
The palette fixture is designed to be easily moved in and out of the tank. Special cone-shaped guides automatically realign with the starting position on the fixture bench.
The material holders are designed to handle various item diameters and withstand tough manufacturing environments. Easy loading and unloading provides an efficient work flow and manufacturing process.
In order to withstand the continual wear of both water and sand, the customised tank and fixture solution is manufactured entirely in stainless steel.
Added value is standard
“Thanks to the customised tank and special fixture solution, our H-model machine is now an enhanced workstation that performs a highly specific and precision production process.”, states Tony Rydh, CTO and founder of Water Jet Sweden. Rydh continues by explaining that “Both the tank and the fixture system are designed for easy operation, and smooth loading and unloading with a specialised forklift. The robust design means durability that can withstand years of cutting in tough manufacturing environments. Finally, it delivers an improved economy and new opportunities for years to come. The easiest way to save material is to stop wasting it!”, concludes Rydh.